All Products
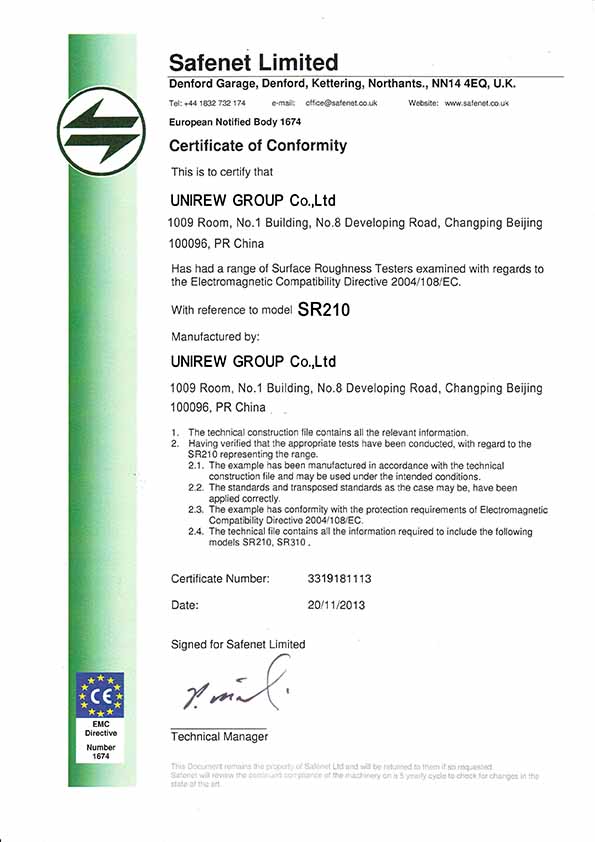
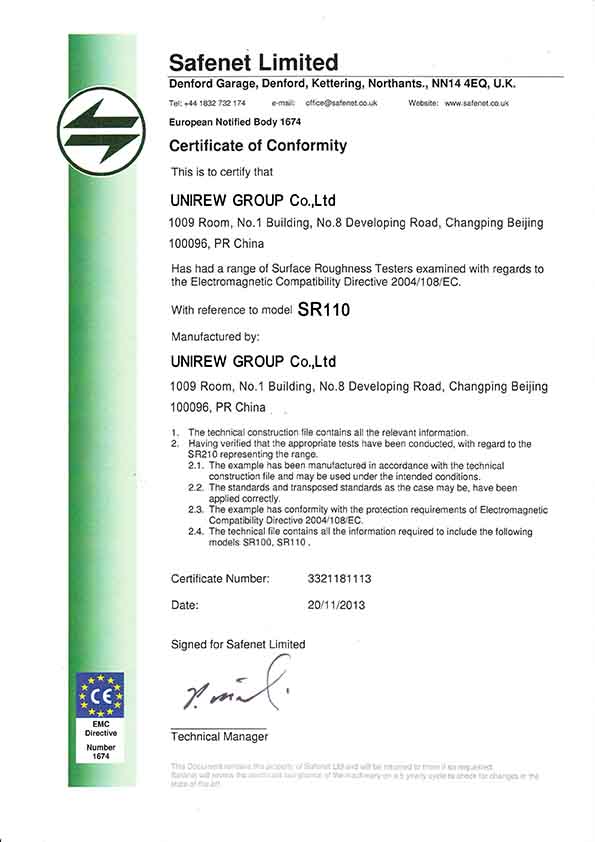
- I'm Online Chat Now
Steel Cord Conveyor Belt Online Real-time Automatic Inspection System
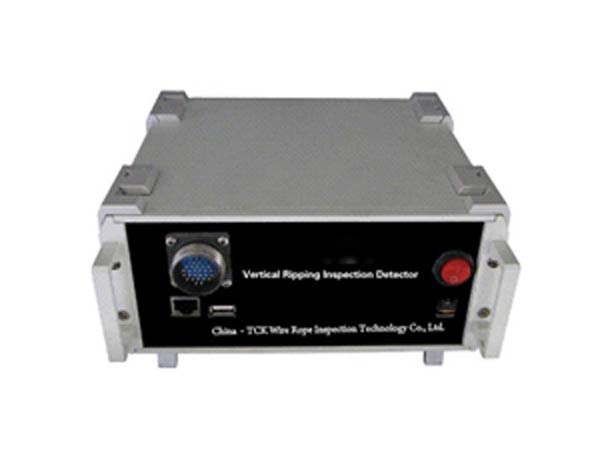


Product Details:
Place of Origin: | PR China |
---|---|
Brand Name: | URNDT |
Model Number: | URNDT Steel cord conveyor belts |
Payment & Shipping Terms:
Minimum Order Quantity: | 1 set |
---|---|
Packaging Details: | Standard export wooden box |
Delivery Time: | Goods in stock,could send out within one week |
Payment Terms: | 100% T/T, Paypal or Wester Union |
Detailed Product Description
I. URNDT System Introduction
URNDT Conveyor Belt Inspection System can achieve the functions of precise positioning of two-dimensional coordinates to splice twitch, internal broken strands, fatigue, corrosion and other defects.
Take adjacent splice as positioning benchmark in the longitudinal direction of conveyor belt, the resolution is 1mm, direct the starting and ending coordinate of defect, position error ≤ 10mm; determine the transverse coordinate of defects according to separate ways on the direction of sensor (A1 ~ A14, B1 ~ B14) corresponding to 100mm partition (1 ~ 13 districts), the position error is also ≤ 10mm.
For example as reflected in the defects records at right image: behind the V8 # splice 49.231 ~ 49.573m of the nine areas range (away from the conveyor belt at the left edge 850 ~ 950mm), showing internal broken cords with values 3, and then by X-ray perspective examination, verifying that there are three broken ropes in the region
(4) Over limit real-time warning prompts
I. URNDT System Introduction
Steel cord conveyor belts, as the important conveying equipment in mining, port, steel mills, and power plants fields, have always been paid much attention by managers for their safety running state. During the operation process of conveyor belt, the splice twitch, broken cords, serious corrosion and other hidden defects might cause serious belt broken accidents. Therefore, users expect to solve the inspection difficulty about safety hidden dangers of conveyor belt urgently.
The successful development of URNDT Conveyor Belt Inspection System creatively proposes a new security monitoring solution, which overcomes the worldwide technical problems. The system can not only accurately detect the hidden dangers such as twitch, displacement of steel cord splice, breakage, fatigue and corrosion, but also reduce the use and maintenance cost of conveyor belt which improves the operation efficiency. So it is the world’s most advantaged steel cord conveyor belt detection equipment.
II. Weak Magnetic Inspection Technology Principle
URNDT Weak Magnetic Inspection Technology, based on “Spatial Magnetic Field Vector Resultants” theory, adopts a new type of electromagnetic-magnetoelectric effect sensors (see figure 1) and achieves a non-destructive testing green technology for the ferromagnetic component.
URNDT high sensitivity sensors are composed of magnetism releasing device and magnetism evaluating device. The magnetism releasing device provides a given weak electromagnetic field Bx, which interacts with the weak magnetic field B of each cross section of the test wire rope. Together they generate the inductive magnetic field By, which the magnetism evaluating device converts the magnetometive force changes of By into electric signals accurately.
Because of the structure particularity of steel cord conveyor belt, URNDT Conveyor Belt Inspection System adopts horizontal + vertical response sensor arrays as the detection device: the horizontal sensors can induct the extent characteristics of metal distribution (the intrinsic component) sensitively, so that achieve the accuracy testing for breakage (including splice), fatigue, abrasion, and corrosion of steel cord through the amplitude output signals from horizontal sensors; while the vertical sensors will be more sensitive for the movement characteristics of metal distribution (the induced component) like splice, breakage…etc open-ended signals. The combination of two kinds of sensors will fully guarantee the positioning and quantitative detection performance.
After sensor arrays pick up the electromagnetic signals of steel cord of conveyor belt, the signals will be converted into digital signals through technical shaping, filtering, and A/D conversion and then input to the 32-bit ARM core; distance-measuring device outputs a pulse signal which will enter the 32-bit ARM interrupt system through anti-shake and equal accuracy tachometer circuit. Both of them take a synchronous spatial domain sampling, and upload the sampling data to the display terminal and large-capacity memory.
Display terminal and detection unit are communicated with each other by industrial Ethernet, compatible with cable or fiber-optic transmission. The Inter Process Communication is adopted unique software architecture and advanced programming techniques to achieve the real time transmission, processing, storage and display of testing data; synchronously support the functions like real time alarm, curve analysis, SMS, image reconstruction and test report print…etc.
III. Technological innovation
High resolution: the instantaneous detection precision value of the steel cord splice displacement can reach 1mm, and can automatically analyze the average and maximum displacement in each operation period. So those accurately and efficiently identify the permanent displacement and elastic displacement of the steel cord splice.
High sensitivity: URNDT sensor (sensitivity: 5V/Gs) is 7000 times more sensitive than Hall element (sensitivity: 7mV/mT under 10V excitation voltage), so it can get a reliable quantitative detection for various early hidden danger like splices twitch, internal breakage, fatigue and corrosion…etc.
Real-time performance of system: Highly integrate the computer, intelligent software and communication technologies together. In the process of on-line quantitative non-destructive testing, the system can take a real time alarm, indicating the safety belt status and showing the holographic perspective image of internal metal structure and defects distribution of the conveyor belt.
Precise positioning: URNDT Conveyor Belt Inspection System adopts horizontal + vertical response sensor arrays which can achieve the two-dimensional precise positioning of internal defects of steel cord conveyor belt; the location error is less than 10×10mm
Image reconstruction: URNDT monitoring software, based on real-time sensor data, dynamically constructs the steel cord image visually. It can take a quantitative and positioning identification for splice displacement, break core, corrosion, abrasion…etc, issue the tips with different colors according to the defect value, and send the warning message.
IV. Schematic Diagram of System Working Process
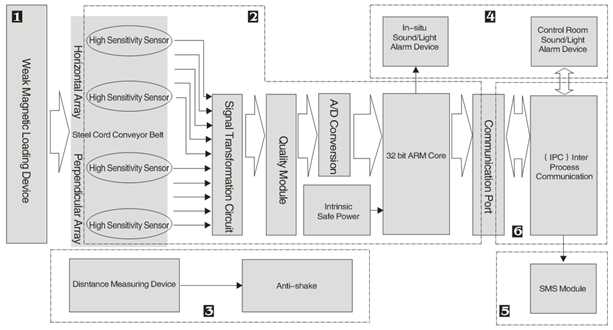
V. System Configuration
IV. Schematic Diagram of System Working Process
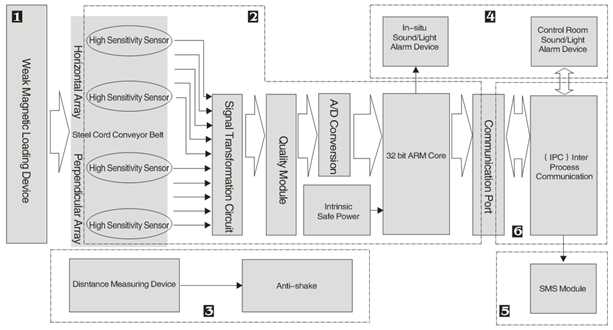
V. System Configuration
URNDT-GMS Weak Magnetic Loading Device
Nd-Fe-B configuration loading module, permanent magnet and intrinsic safe design
Wide-space and non-contact loading, Zero release and Zero energy
Modular units can be suitable for different specifications of steel cord conveyor belt
Stainless steel frame structure with the rain-proof, shock-proof, and oil-proof performance
All-weather operation and daily maintenance-free
URNDT-GMS flameproof and intrinsically safe type testing unit
Built-in horizontal + vertical weak magnetic sensor spatial response arrays
Embedded low-power 32-bit industrial CPU, high speed data acquisition system, and large capacity storage
Modular units can be suitable for different specifications of steel cord conveyor belt and installed very easily
Wide-space and non-contact will make no affect of the normal production during the inspection
High-strength copper explosion-proof housings, stainless steel connecting brackets, on-line installation and automatic operation, daily maintenance-free
URNDT-GMS Distance Measuring Device
Adopt high-precision explosion-proof photoelectrical encoder and light aluminum frame
Anti-loosening mechanical structure, self-clamp-floating cantilever support, and friction wheel with multi-channel anti-slip rings ensure reliably distance measuring
Integrated anti-shake, pulse shaping, and other industrial designs, stable signal and high accuracy distance measurement
URNDT Self-controlled sound/light alarm device
In line with GB3836-2000 “Electrical Apparatus for Explosive Gas Atmospheres” standard, with mining product safety signs Exd[ib]I explosion-proof and intrinsically safe products
Give the warning indication for the safety state of conveyor belt according to test data by EPLD phototube, DDY-6 buzz alarm and software control component
Green Light: Steel cord conveyor belt is in safe condition
Yellow Light: Steel cord conveyor belt has partial hidden dangers, and need to be monitored and maintained more intensively
Red Light: Steel cord conveyor belt is in extremely dangerous condition and should be shut down immediately and emergency plan should be executed, such as changing new belt…etc
URNDT SMS safety report function device
Based on the real-time monitoring results and historical statistics, the alarm information will be showed and locked in terminal interface. The corresponding alarm information can be remotely sent to manager’s mobile phone by SMS according to the system pre-lock.
URNDT multi-channel terminal main control device
Multi-channel step-by-step calling, synchronous and high speed data receiving & sending operation mode
Optional configuration for wire/wireless communication and cable/fiber access
Touch screen computer supports B/S (browser and server) dialogue operation mode
Windows platform, URNDT designed command and control system software which supports multi-language user interface
Target archiving management system, FIFO data structure, available on-line real time collection, analysis and processing of testing data of conveyor belt
Reconstruct objective dynamic perspective image according to testing data
Synchronous segmented display of 14-channel signal curve
Real-time sound/light alarm and remote SMS report
Support testing data retrieving and test report printing whenever needed
Test data self-evaluation system
Intelligent self-learning function
Self-diagnosis function for system fault and manual/auto switch operation mode
Compatible with the LAN or public network for information sharing
Embedded remote takeover capabilities that enables whole system remote debugging, maintenance and interaction
Provide a temporal trend analysis for various hidden dangers of conveyor belt, and scientifically evaluate safety state of conveyor belt
VI. URNDT Models and Inspection Range
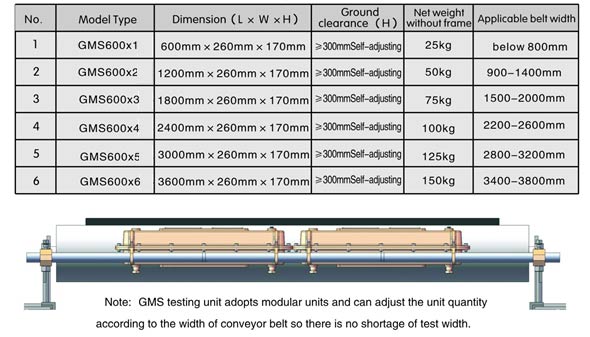
VII. System Functions
Capable of fulfilling real-time inspection on four major hidden dangers including horizontal breakage and vertical ripping
URNDT Conveyor Belt Inspection System, adopting unique signal processing models and feature recognition algorithms, can automatically identify the splice order of steel cord and number the splices automatically simultaneously; users can label the number of splices in accordance with customary in order to compare history maintenance records.
URNDT Conveyor Belt Inspection System, based on the real-time inspection data to the same splice, automatically sum up the maximum displacement and the average amount of displacement in the specified amount of time, so the user can easily determine the magnitude range of splice elastic displacement, and can also compare the average amount of displacement in different periods, so that the severity of the permanent displacement can be determined accurately.
(3)Quantitative and locating test for broken strands, corrosion, and fatigueVI. URNDT Models and Inspection Range
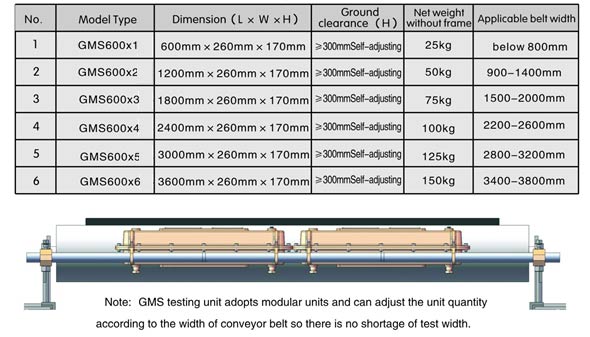
VII. System Functions
Capable of fulfilling real-time inspection on four major hidden dangers including horizontal breakage and vertical ripping
Quantitative and positioning inspection on steel cord splice displacement
Quantitative and positioning inspection on steel cord breakage
Quantitative and positioning inspection on steel cord corrosion
Positioning inspection on vertical ripping of steel cord conveyor belt
Operation status report system by text message
Technical Parameters
(2) Splice twitch, qualitatively and quantitatively testing for spliceTechnical Parameters
System parameter
1. Sensor sensitivity:A = 2.5~5V/G
2. Space distance between testing head and conveyor belt:50~110mm
3. Sampling response frequency:8kHz
4. Data transmission rate:10M/100Mbps Self-adaptive
5. Underground power supply:AC127V±10%/50Hz,Max power:3W/Unit
6. Ground power supply:AC220V±10%/50Hz,Max power:600W
System performance parameter
7. Positioning accuracy:1mm
8. Splice displacement inspection accuracy (non-elastic change):>95%
9. Internal broken core inspection accuracy:99%
10. Inspection accuracy for steel cord fatigue and corrosion:>90%
11. Fault locating error
Locating error in horizontal direction:±100mm
Locating error in vertical direction:±50mm
System adaptability parameter
12. Inspection belt speed:0~8m/s
13. Single unit inspection width:600mm±200mm
14. Signal transmission distance
Distance with cable access:≤80m(1km with a relay server)
Distance with Fiber access:≤10km
15. Sensor working temperature
Temperature:-20℃~+50℃
Humidity:≤95%RH
System Optimization and Accessibility Options
16. Automatic identification of belt splice sulfurization grade (note: there are 4 sulfurization grades of belt splice)
17. Automatic numbering function for steel cord splice
18. Real-time sound/light alarm function
19. Real-time or pre-set SMS remote reporting function
20. Real-time data compression and image reconstruction technology
21. Auto-evaluation system and self-learning function
22. System self-diagnosis function
23. Remote takeover, debugging and maintenance function
IX. Installation Scheme
Due to the modular design, URNDT Conveyor Belt Inspection System can simultaneously monitor four steel cord conveyor belts for their safe operation conditions, not only to independent monitoring of the entire conveyor belt, but also to meet the centralized monitoring of a number of conveyor belts according to customer request. The system has a simple structure, easy installation, stable operation, reliable performance, hardware and software have a good versatility and scalability.
Take the above figure as an example, 1. Loading device installed in the lower belt; 2. Testing unit also installed in the lower belt but behind loading device; 3. Distance Measuring Device installed at the upper surface of lower belt. As long as the return lower belt is flat belt and run more smoothly, we can facilitate the achievement of fixed installation; 4. Sound/light alarm; 6. Terminal control center installed in the controlling room.
X. Professional Software for URNDT Online Real-time
Automatic Inspection System for Conveyor Belt
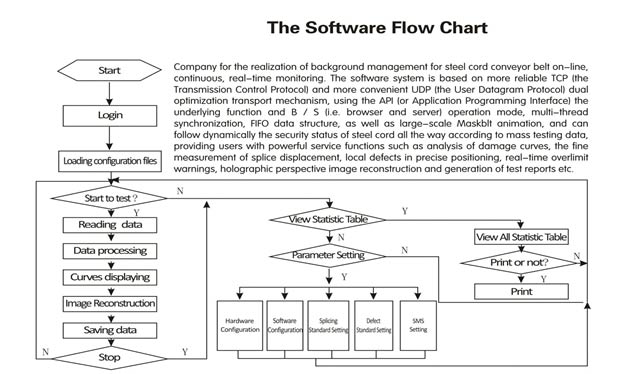
(1) Holographic perspective image reconstruction
For the complex components like steel cord conveyor belt only damage curve display still can not intuitively reflect the overall impact on the safety performance of conveyor belt acted by every local flaw. As the URNDT detection technology advances, URNDT Conveyor Belt Inspection System can provide users with more complete and intuitive internal image reconstruction functionality of conveyor belt.
X. Professional Software for URNDT Online Real-time
Automatic Inspection System for Conveyor Belt
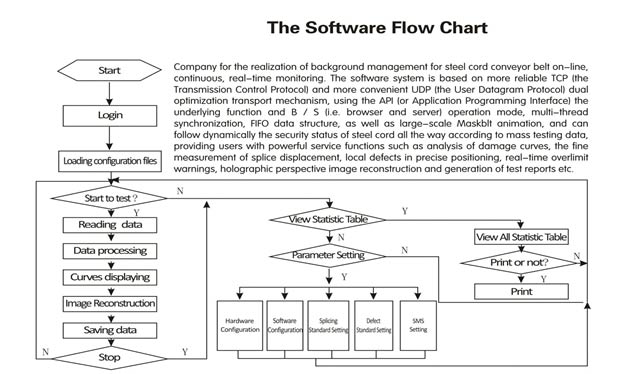
(1) Holographic perspective image reconstruction
For the complex components like steel cord conveyor belt only damage curve display still can not intuitively reflect the overall impact on the safety performance of conveyor belt acted by every local flaw. As the URNDT detection technology advances, URNDT Conveyor Belt Inspection System can provide users with more complete and intuitive internal image reconstruction functionality of conveyor belt.
The conveyor belt images delivered by URNDT Conveyor Belt Inspection System is a holographic perspective image which is generated through the rehabilitation of real-time detection data dynamically, based on the actual form of on-site conveyor belt. The image displays the steel cord structure and defect distribution inside the steel cord conveyor belt, not only labeling in heavy color planimetric position of the faults but also reflecting the damage degree of steel cord by way of mouse remark, prompting real-time dangerous information.
URNDT Conveyor Belt Inspection System, adopting unique signal processing models and feature recognition algorithms, can automatically identify the splice order of steel cord and number the splices automatically simultaneously; users can label the number of splices in accordance with customary in order to compare history maintenance records.
URNDT Conveyor Belt Inspection System, based on the real-time inspection data to the same splice, automatically sum up the maximum displacement and the average amount of displacement in the specified amount of time, so the user can easily determine the magnitude range of splice elastic displacement, and can also compare the average amount of displacement in different periods, so that the severity of the permanent displacement can be determined accurately.
URNDT Conveyor Belt Inspection System can achieve the functions of precise positioning of two-dimensional coordinates to splice twitch, internal broken strands, fatigue, corrosion and other defects.
Take adjacent splice as positioning benchmark in the longitudinal direction of conveyor belt, the resolution is 1mm, direct the starting and ending coordinate of defect, position error ≤ 10mm; determine the transverse coordinate of defects according to separate ways on the direction of sensor (A1 ~ A14, B1 ~ B14) corresponding to 100mm partition (1 ~ 13 districts), the position error is also ≤ 10mm.
For example as reflected in the defects records at right image: behind the V8 # splice 49.231 ~ 49.573m of the nine areas range (away from the conveyor belt at the left edge 850 ~ 950mm), showing internal broken cords with values 3, and then by X-ray perspective examination, verifying that there are three broken ropes in the region
(4) Over limit real-time warning prompts
The real-time alerting functions of URNDT Conveyor Belt Inspection System, is divided into sound and light alarm and SMS alarm from the alarm form, and alarm at any time and appointment alarm from alarm sending device.
Sound and light alarm, mainly for on-site inspections and main control room, users could check specific cause for alarm accordingly.
Test message reporting, designed for equipment supervising department or the persons in charge of safety operation; one time setting, ready to send daily report for equipment safety status automatically
Real-time alarm, the system can issue a warning immediately based on presetting for over limit defects if over-limit defects (Medium or Severe level) detected
Appointment alarm: the system can generate a report based on analyzed results and send corresponding information at a scheduled time point.
(5) Defect Curves Display And Analysis
URNDT Conveyor Belt Inspection System is capable of displaying holographic curves by adopting the technology of large-capacity memory and dynamic data processing.
The following diagram shows the holographic waveform curve of steel cord conveyor belt from a main shaft of a coal mine, which can intuitively display there are 22 splices in total and among them there are 2 new vulcanized splices with close distance; also show the unusual signal curves in the non-splice area.
(6)History records review and print & History curves playback
The function facilitates equipment managers to keep abreast of the historical evolution of internal defects in the process of carrying out the trend analysis of conveyor belt safety performance.
(7) Print Test Report
In addition to curves and images displaying, URNDT Conveyor Belt Inspection System also provides users with more concise test reports, including major inspection conclusions from system data analysis and processing, statistical data tables, as well as the input information, which are informative, concise and intuitive and very easy to compare and analyze for managers.
In addition to curves and images displaying, URNDT Conveyor Belt Inspection System also provides users with more concise test reports, including major inspection conclusions from system data analysis and processing, statistical data tables, as well as the input information, which are informative, concise and intuitive and very easy to compare and analyze for managers.
(8) Th system is capable of remoting take-over and after-sales service
System can access to the LAN / public network platform, and be embedded in remote take-over function. Easy remote debugging, software upgrades, fault diagnosis and other after-sales service functions. As long as the user needs, the remote take-over can be achieved via the Internet and other services like online commission, maintenance.
XI. Product Applications
System can access to the LAN / public network platform, and be embedded in remote take-over function. Easy remote debugging, software upgrades, fault diagnosis and other after-sales service functions. As long as the user needs, the remote take-over can be achieved via the Internet and other services like online commission, maintenance.
XI. Product Applications
URNDT Steel Cord Conveyor Belt Online Real-time Automatic Inspection System has been widely used in industries such as Mining, Ports, Steel Mills, and Power Plants.
XIII. URNDT Vertical Ripping Inspection Detector
XIII. URNDT Vertical Ripping Inspection Detector
URNDT vertical ripping inspection detector is the inspecting and protective equipment for the operating conveyor belt. When the conveyor belt is ripped by unexpected particles, the detector will pick up the signal in real time and send an alarm signal to the electric relay to stop the conveying operation. Under this procedure, the safe conveying operation is guaranteed.
Considering avoiding the frequent maintenance, the URNDT vertical ripping inspection detector is installed under the returning belt, firm to the frame. And the structure can be flexibly modified.
Contact Details
|
- Other Products
URNDT MT-250 Demagnetizer
MJE-Yoke Series Magnetic Particle Flaw Detector
Metis Y Series Magnetic Particle Flaw Detector
Metis P2 Permanent Magnet Flaw Detector
Metis P1B Permanent Magnet Flaw Detector
Metis P1 Permanent Magnet Flaw Detector
URNDT 1012MA Wireless Portable Flat Panel Detector for 320KV DR System
IDEA-IT24ET Multi-frequency Remote Field Eddy Current Tester